|
Fireproof Cables
|
|
|
News
1.New revision of fire resistant cable test standard published~
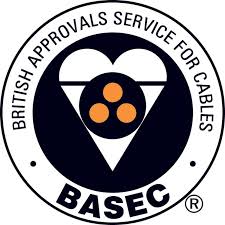
Toughest tests prevail as British Standards streamline testing method.
BS 6387 is a long-established British Standard that defines methods for testing an electrical cable’s resistance to fire. The cable needs to maintain circuit integrity under specific fire conditions, meaning it must not short circuit, stop working, nor suffer loss of continuity. This standard is only relevant to a certain type of cable – those not exceeding a 600/1000 volt rating, with an overall diameter less than or equal to 20mm, and it doesn’t include single core cables. The previous edition of the BS 6387 standard was published in 1994 (known as BS 6387:1994) and detailed eight fire performance categories that the cable could be tested against. On December 31st 2013, a full revision of the standard was published, BS 6387:2013, and it now retains only the three most stringent categories for the fire resistant characteristics of the cables – the three toughest tests to pass!
In a real-life situation, these types of cable are used throughout buildings such as hospitals, schools, shopping centres, stadiums and high rise buildings, supplying electricity to critical systems such as emergency lighting, fire alarms, computer systems and voice evacuation controls. All these evacuation and communication systems require electrical power and control circuitry to remain fully functional throughout a potentially serious fire that could rage for many hours. Therefore, it is vital that power supplies remain intact for a sufficient period to help occupants vacate the building as quickly as possible and to assist the fire brigade in tackling the fire. Although they may be small cables, they need to be robust not only to fire, but also to impact damage and the effects of water spray from fire sprinklers or fire-fighting operations.
Testing and certification bodies cannot test cables for every fire-related eventuality. However, by having consistent testing methods detailed in standards such as BS 6387:2013, this ensures that cable products provided by manufacturers for test can be directly compared to ensure performance is benchmarked. This new revision was co-written and approved by a committee of a dozen different organisations including cable manufacturers, material suppliers, testing and certification bodies, and fire alarm system manufacturers.
The new test method
BS 6387:2013 now specifies that the cable has to pass each of the three fire tests C, W and Z. At the time of the test, each cable is set up within a specialised fire testing facility and is energised to 600V while connected to a number of light bulbs and fuses. This provides the test technician a visual indicator that the cable can sustain performance in the fire tests, or not. Separate test pieces from the same sample of cable are tested to each of these three protocols:
C test
This is a fire-alone test at the highest temperature, for the longest time.
Temperature of attack: 950°C ±40°C
Time: 3 hours
W test
This is a fire and water test simulating a sprinkler system.
Temperature of attack: 650°C ±40°C
Time: 15 minutes fire and 15 minutes sprinkler
Z test
This is a fire test with an indirect mechanical shock.
Temperature of attack: 950°C ±40°C
Time: 15 minutes of fire with impact every 30 seconds
In the previous standard BS 6387:1994 there were another five lower-level tests as well as C, W and Z tests. However, C, W and Z are the hardest tests to pass and most cables marketed have adopted these grades – the other lower grades have not been widely used. Also, additional electrical and mechanical cable tests have been removed from BS 6387, leaving only the three C, W and Z fire test protocols.
Not as clear-cut for cable manufacturers
Cable manufacturers need to be aware that the BS 6387:2013 revision is now in force and it will affect cable manufactured from 2014 forward. It also has implications on what manufacturers can legitimately claim.
With the removal of the five lower-level fire tests and the other cables tests from the standard, certain grades of cables or custom-designed cables will no longer have a recognised standard against which they can be tested and approved. This means that cable manufacturers will now need to set their own specifications for these cables. As an example, this will affect fire resisting, single core insulated wires e.g. with a mica tape layer, for which no cable design standard currently exists.
This standard also affects cables under BS 7629 Part 1. These cables are defined as ‘electric cables 300/500V fire resistant screened cables having low emission of smoke and corrosive gases when affected by fire’. One of the test specifications within this standard is BS 6387.
BS 7846:2009, which is a design standard for armoured fire-resistant power distribution cables currently refers to the superseded issue of BS 6387:1994 as part of the test regime for ‘F2’ level of fire resistance. It appears likely that a future revision of BS 7846 will be changed to refer to the revised issue of BS 6387.
The problem arises if the cable is marked with BS 6387 and this is not dated. A cable manufacturer with BS 6387:1994 cannot claim it is BS 6387 if the cable has not been tested or certified to BS 6387:2013. It will affect all cable manufacturers including international manufacturers with approvals to the 1994 edition. They need to be aware of the change whether they are selling into the UK or across the world. The knock-on effect is that if they are selling cables under BS 7629 specification they have to recognise that BS 6387 has changed.
If the cable is BASEC approved then the new test method BS 6387:2013 will be used in follow-up surveillance assessments, so cable manufacturers won’t have to worry. However, if the cable is tested or approved by another body and has previously been printed BS 6387 (undated) on the cable, then the manufacturer is advised to contact that body for advice.
In common with questions raised when other standards have been updated, industry participants from manufacturers to installers need to know whether the change renders existing stock unsaleable. Since existing stock would have been tested in accordance with the issue of BS 6387 prevailing at the time of manufacture, there is no reason not to use the stock until it is exhausted. Furthermore, as there are no technical differences between the performance categories C, W and Z between the 1994 and 2013 editions, there will be no changes to cable performance. However, again, a non-dated reference to BS 6387 on the cable is potentially misleading and should no longer be claimed.
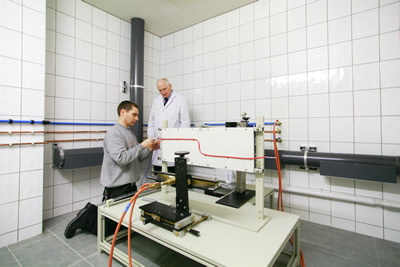
In all instances where there is some confusion, it is advised to speak to the test and certification body or trade association for advice relevant to the particular situation.
BS 6387’s bigger brother
As mentioned previously, BS 6387:2013 is applicable to cables of rated voltage not exceeding 600/1000V and not exceeding 20mm in diameter. In a real building however, the incoming power supply cables are likely to be much larger and less flexible, often armoured. Having developed BS 6387 for smaller cables, the British Standards committee also developed BS 8491:2008, for assessing the fire performance of power cables as components for smoke and heat control systems and certain other active fire safety systems within building to complete the fire–resistant system. This standard is for the assessment of cables of the same voltage but greater than 20mm diameter. In order to accommodate these larger cables the tests are not identical as those stipulated in BS 6387, however they still incorporate direct fire attack, mechanical shock and water spray, over various durations up to two hours. More severe fire tests have been and are being developed to assist architects and fire engineers in achieving higher levels of safety in buildings using active fire protection such as smoke control and extraction systems, which rely on continuity of power supply during a fire.
There has been controversy over the seemingly arbitrary cut-off for both BS 6387 (largest size) and BS 8491 (smallest size) at 20mm OD. BASEC has sympathy with manufacturers wishing to test smaller OD cables to the more severe test, BS 8491, such as mineral insulated cables, and likewise for those wishing to extend BS 6387 to larger cables or cables with different designs that are currently excluded. However, these tests are aiming to provide reassurance about fire performance for two quite different groups of cables, respectively, lighter duty control cables and heavy power distribution cables.
At the same time, architects, fire engineers and designers across the world are taking advantage of new technologies to produce innovative designs incorporating more elaborate layouts in buildings, and require more effective fire performance systems. As buildings become more complex in this way, the need for higher performance cables has been identified by a number of manufacturers.
BASEC is frequently asked about ‘low smoke halogen free’ (LSHF, and many other similar acronyms) cables, and the requirements for this categorisation. To describe a cable as ‘LSHF’, it must generally pass two tests: (a) a smoke cube test, which sets a maximum accumulated smoke density produced when burning the cable with a standard fire, and (b) a corrosive and acid gas test (also referred to as assessment of halogens) where the cable materials are roasted in a tube furnace and must give off a maximum of 0.5% acid gas. These tests are both specified in the relevant cable standards which include the description ‘having low emission of smoke and corrosive gases when affected by fire’. Cables made from PVC or similar halogenated materials are unlikely to pass these tests. A common misunderstanding is that an ‘LSF’ cable means it has only passed the smoke test and not the acid gas test. In reality, many of these marketing terms are essentially meaningless unless they are clearly associated with test requirements.
CPR to include cables in remit
Looking into the not too distant future we have a potential shake-up within Europe when the Construction Product Regulation (CPR) is extended to include cables within its remit. At the present time CPR applies to many building materials, and is the construction industry’s most significant change in how construction products are sold within Europe. From 1 July 2013, under the Construction Products Regulation (CPR) 2011, it became mandatory for manufacturers to apply CE marking to any of their products which are covered by a harmonised European Standard (hEN) or European Technical Approval (ETA). This was a major change, as affixing a CE marking under the provisions of the previous Construction Products Directive (CPD) was voluntary. Once the CPR requirements become effective for cables, there will be additional requirements to a number of standards, including standards for fire resistant cables, to be aware of. Initially this will see new requirements and grading for reaction to fire. The inclusion of a further new test for fire resistant cables (P-class) is already well advanced, but this is unlikely to replace the need for standards like BS 6387 or BS 8491, which address specific local design and performance needs.
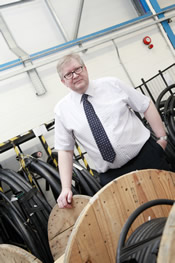
This article is attributed to Dr Jeremy Hodge, chief executive of the British Approvals Service for Cables (BASEC) (Above)
For more information on BASEC's work please visit their independant websitehttp://www.basec.org.uk/ |
|